Proposal for Geodyn Solutions: Waste Tire Pyrolysis-to-Energy Factory
Construction and Operation of a 300 MT/Day Waste Tire Pyrolysis Facility for Electricity Generation
Executive Summary
Geodyn Solution proposes a cutting-edge facility to process 300 metric tons (MT) of waste tires daily using advanced pyrolysis technology optimized for maximum bio-oil and syngas production. These outputs will fuel a gas turbine and ORC system to generate ~15–18 MW of electricity, sold at $0.17/kWh. This project tackles waste tire disposal while delivering renewable energy, with an estimated capital expenditure (CAPEX) of $40–50 million and annual operational expenditure (OPEX) of $7–9 million. The factory is projected to achieve a return on investment (ROI) within 4–6 years, with a net present value (NPV) of $25–35 million over 15 years, assuming operational efficiency and stable electricity demand.
Project Overview
Objective:
- Convert 300 MT/day of waste tires into bio-oil (~150 MT/day) and syngas (~120 MT/day) using high-yield pyrolysis.
- Utilize all bio-oil and syngas to generate electricity via a turbine-ORC system for sale at $0.17/kWh.
- Maximize energy output and sustainability with a strong ROI.
Process Description:
- Feedstock Preparation: Waste tires are shredded into 50–100 mm chips.
- Pyrolysis Technology: A fast pyrolysis system with a fluidized bed reactor at 500–600°C is employed to maximize bio-oil and syngas yields:
– Bio-oil: ~50% yield (150 MT/day), high energy content (~18 MJ/kg).
– Syngas: ~40% yield (120 MT/day), calorific value ~18 MJ/Nm³.
– Char: ~10% (30 MT/day), minimal focus, used as low-grade fuel or disposed.
– Steel: ~10% (30 MT/day), sold as a by-product. - Energy Generation:
– Bio-oil is combusted in a boiler to produce steam for a turbine (~10 MW).
– Syngas powers a gas turbine (~5–6 MW), with waste heat recovered via ORC (~2–3 MW additional).
– Total output: 15–18 MW continuous. - By-Product Handling: Steel is sold; char is repurposed or landfilled.
Technology Choice: Fast pyrolysis with a fluidized bed reactor is selected for its high liquid (bio-oil) and gas (syngas) yields, proven in biomass and tire applications. Catalysts (e.g., zeolites) may enhance syngas quality, optimized during engineering design.
Factory Design and Size
Facility Requirements:
– Land Area: 8–12 acres (32,000–48,000 m²).
– Pyrolysis reactors: 8,000 m².
– Turbine, boiler, and ORC system: 6,000 m².
– Storage (tires, bio-oil): 10,000 m².
– Ancillary facilities: 4,000 m².
Equipment:
– Shredders (2 units, 150 MT/day each).
– Fluidized bed reactors (3 units, 100 MT/day each).
– Gas turbine (5–6 MW), steam turbine (10 MW), ORC unit (2–3 MW).
– Bio-oil boiler and syngas cleaning system (scrubbers, filters).
– Utilities: Water (cooling), electricity (startup), thermal oil (heat transfer).
Location Considerations: Near tire supply, grid access, and transport hubs.
Production Outputs
Yields (based on fast pyrolysis):
- Bio-Oil: 150 MT/day (50%), energy content ~18 MJ/kg.
- Syngas: 120 MT/day (40%), ~48,000 Nm³/day, ~18 MJ/Nm³.
- Char: 30 MT/day (10%), ~15 MJ/kg (minor fuel use).
- Steel: 30 MT/day (10%), market price ~$200/MT.
Electricity Generation:
- Bio-Oil: 150 MT × 18 MJ/kg = 2,700 GJ/day.
- Boiler-turbine efficiency: ~35%.
- Output: 2,700 GJ × 35% ÷ 86,400 s/day = ~10 MW.
- Syngas: 48,000 Nm³ × 18 MJ/Nm³ = 864 GJ/day.
- Gas turbine efficiency: 35% + 10% ORC = 45%.
- Output: 864 GJ × 45% ÷ 86,400 s/day = ~5–6 MW + 2–3 MW ORC = 7–9 MW.
- Total Output: 15–18 MW continuous.
- Annual Output: 15–18 MW × 8,000 hours/year = 120,000–144,000 MWh/year.
Capital Expenditure (CAPEX)
Estimated Cost Breakdown:
– Equipment: $25–30 million (reactors, turbines, ORC, boiler).
– Construction: $10–12 million (buildings, infrastructure).
– Engineering & Permitting: $3–5 million.
– Contingency: $2–3 million.
– Total CAPEX: $40–50 million.
Operational Expenditure (OPEX)
Annual Costs (330 days/year):
– Feedstock: $30/MT × 300 MT/day × 330 days = $2.97 million (offset potential via tipping fees).
– Labor: 45 employees × $50,000/year = $2.25 million.
– Utilities: $1–1.5 million (water, startup power).
– Maintenance: 3% of CAPEX = $1.2–1.5 million.
– Overhead & Misc.: $0.5–1 million.
– Total OPEX: $7–9 million/year.
Revenue Projections
Annual Revenue (330 days/year):
– Electricity: 120,000–144,000 MWh × $0.17/kWh = $20.4–24.48 million.
– Steel: 30 MT/day × $200/MT × 330 days = $1.98 million.
– Total Revenue: $22.38–26.46 million/year.
Net Profit:
– Revenue: $22.38–26.46 million/year.
– OPEX: $7–9 million/year.
– Annual Profit: $13.38–19.46 million (pre-tax, pre-depreciation).
Return on Investment (ROI)
– Payback Period:
– CAPEX: $40–50 million.
– Annual Profit (after tax, ~30%): $9.37–13.62 million.
– Payback: $40M ÷ $13M ≈ 3 years; $50M ÷ $9.37M ≈ 5.3 years.
– Adjusted for financing/depreciation: 4–6 years.
– Net Present Value (NPV):
– 15-year horizon, 8% discount rate, $15–18M annual cash flow: ~$25–35 million.
– Internal Rate of Return (IRR): Estimated 18–25%.
Critical Assumptions & Risks
– Assumptions: Stable electricity price, 90% uptime, consistent tire supply.
– Risks:
– Lower-than-expected bio-oil/syngas yields.
– Regulatory changes impacting emissions or waste processing.
– Grid connection delays.
– Mitigation: Pilot testing for yield validation, long-term power purchase agreements, modular design for scalability.
Conclusion & Recommendation
This 300 MT/day waste tire pyrolysis-to-energy factory leverages fast pyrolysis to maximize bio-oil and syngas for electricity generation, delivering 15–18 MW of power and ~$22–26 million in annual revenue. With a CAPEX of $40–50 million and OPEX of $7–9 million/year, ROI is achievable in 4–6 years. Geodyn Solution should conduct a pilot study to confirm yields, secure grid access, and finalize financing to advance this sustainable, high-return project.
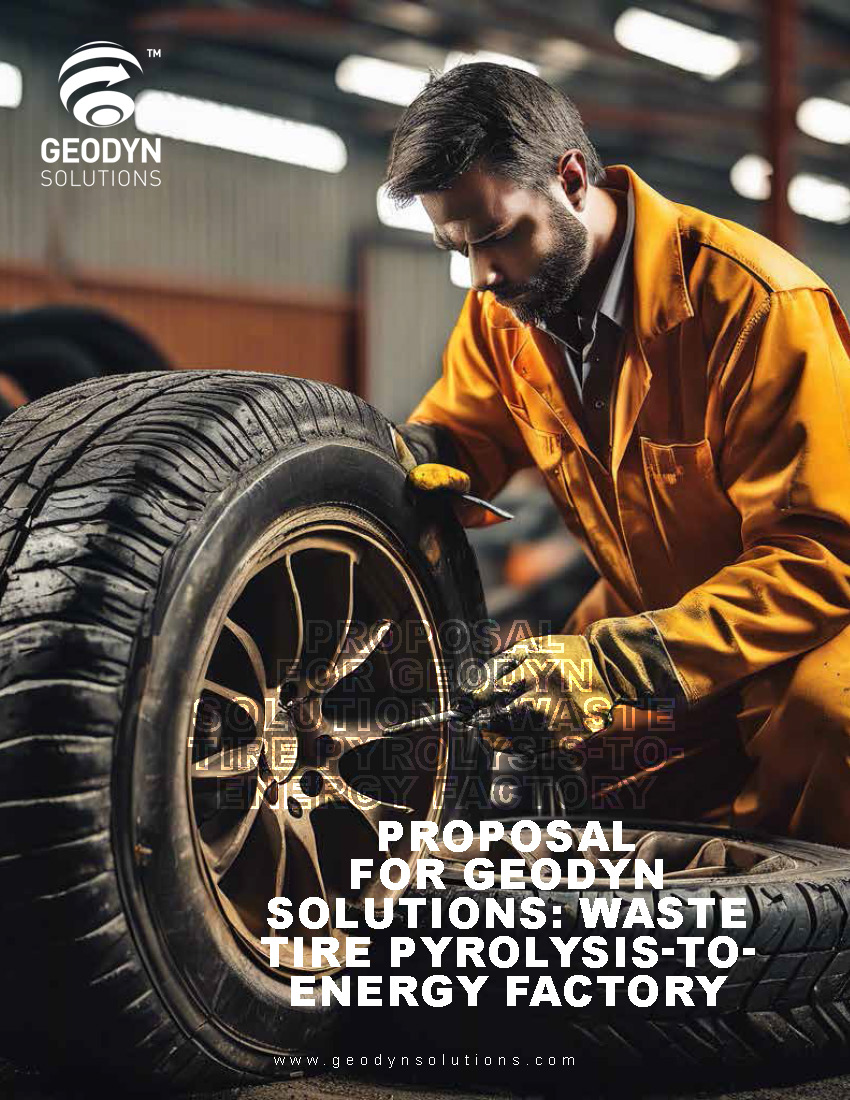
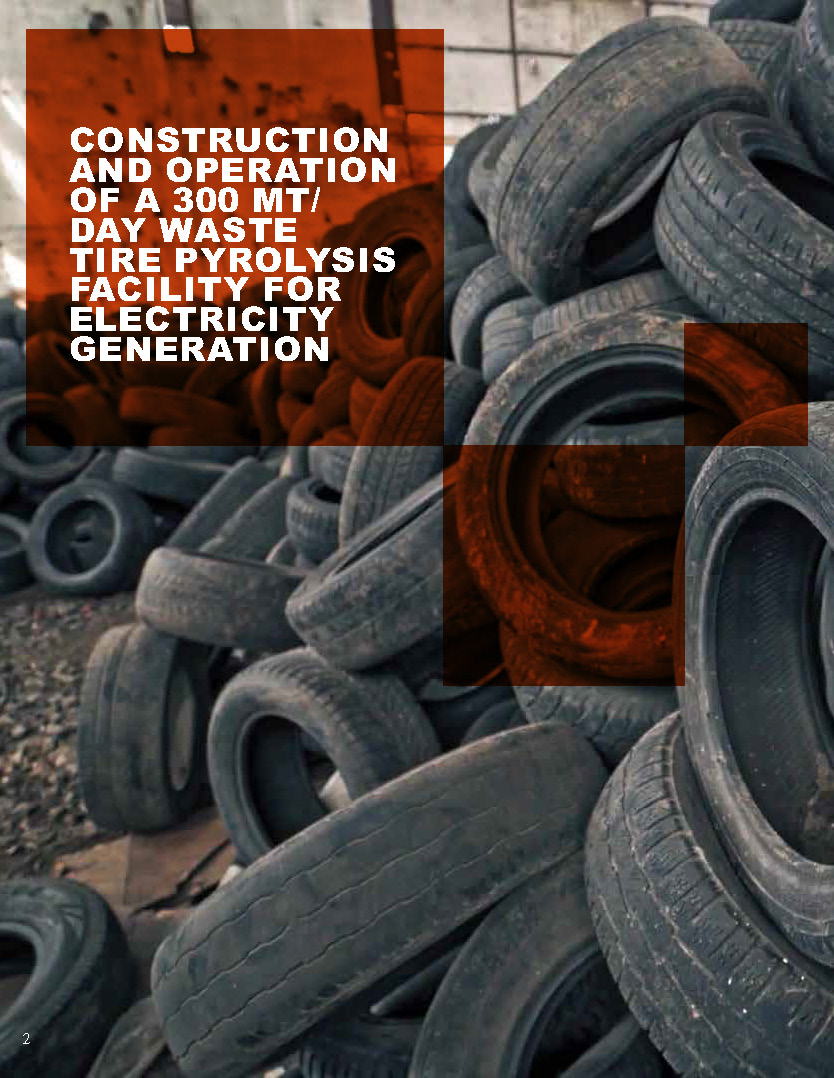
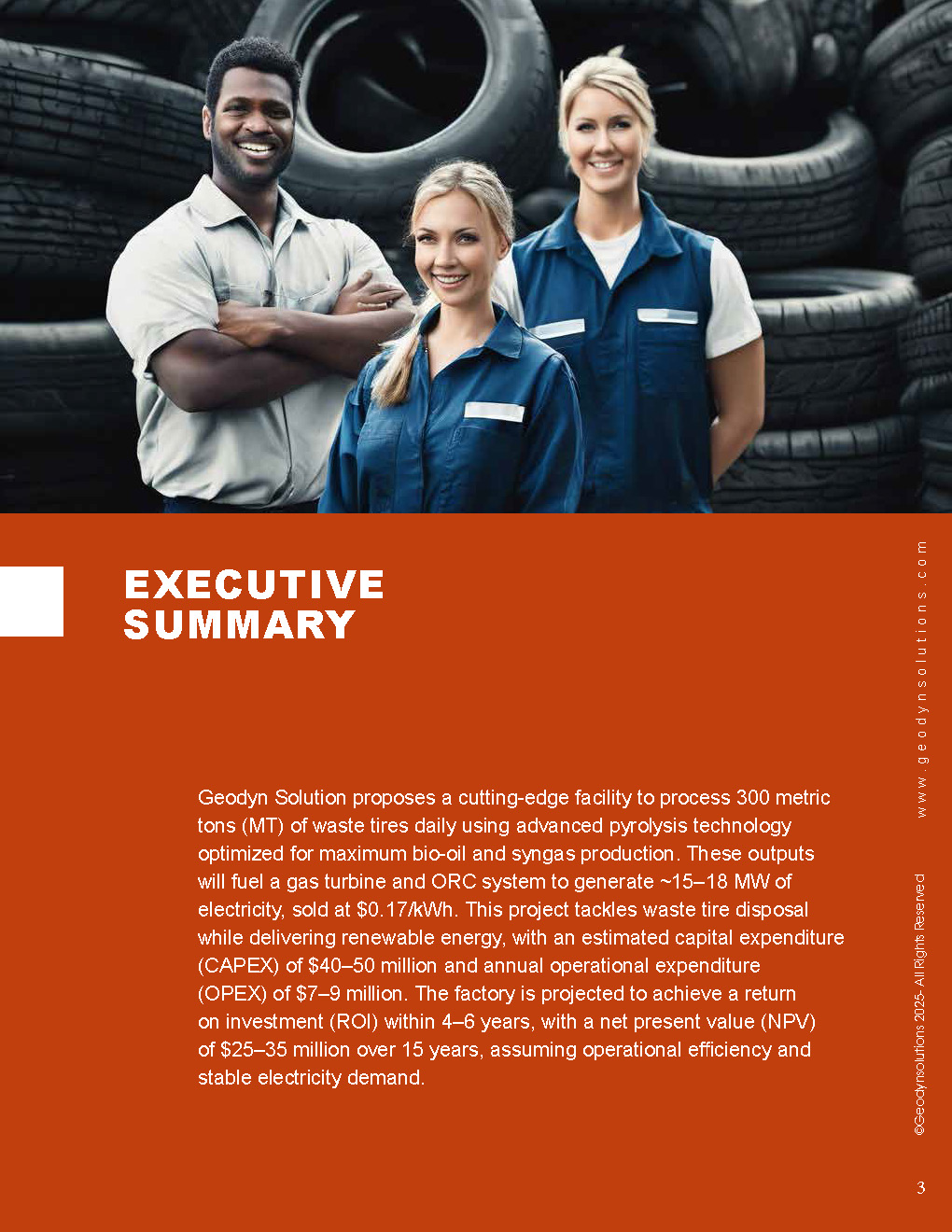
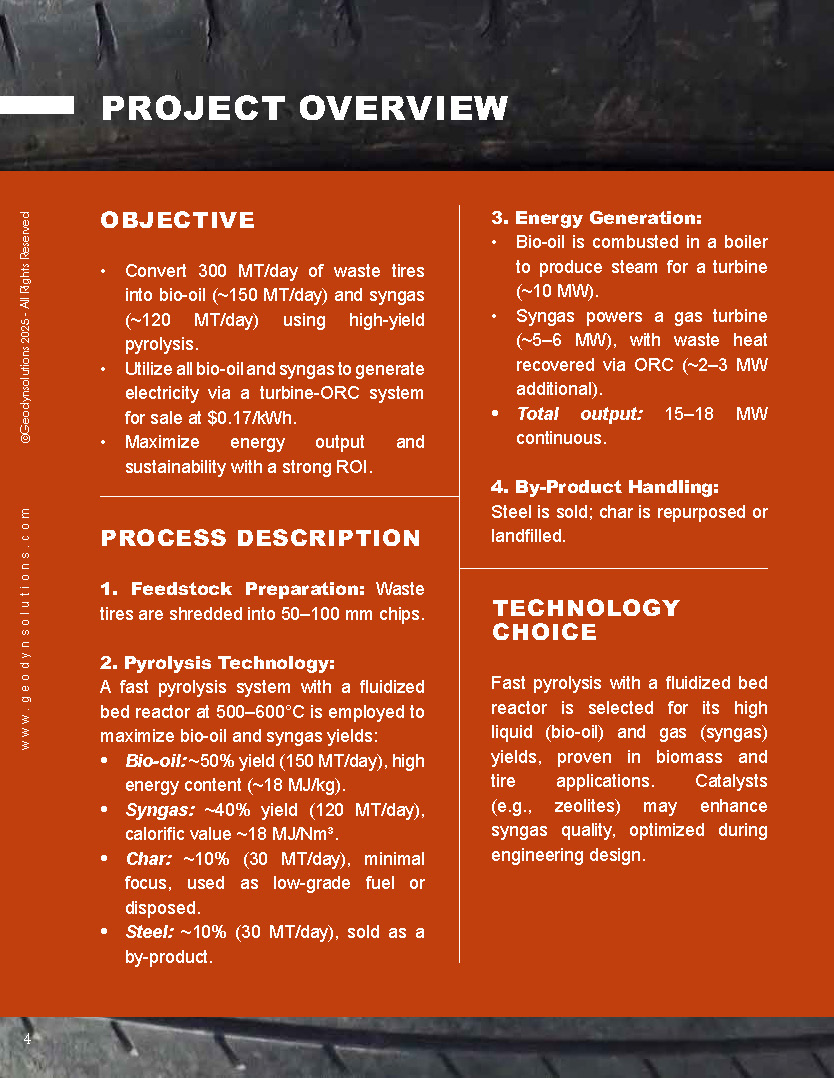
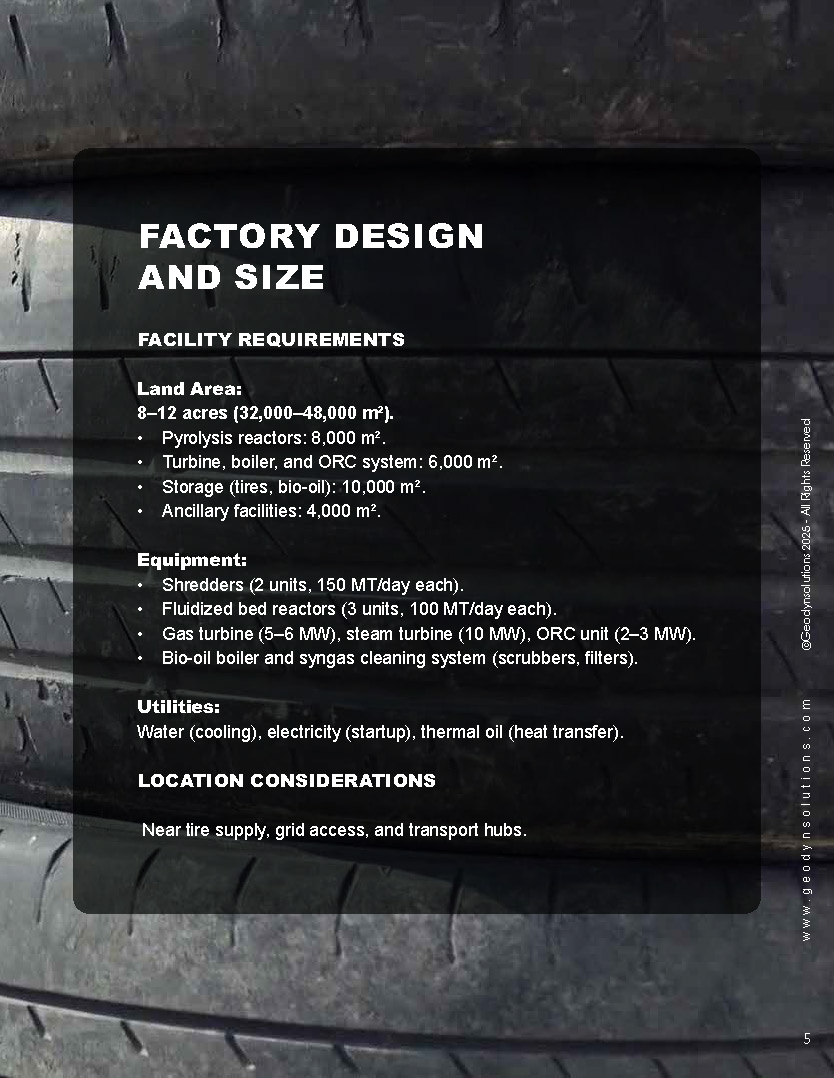
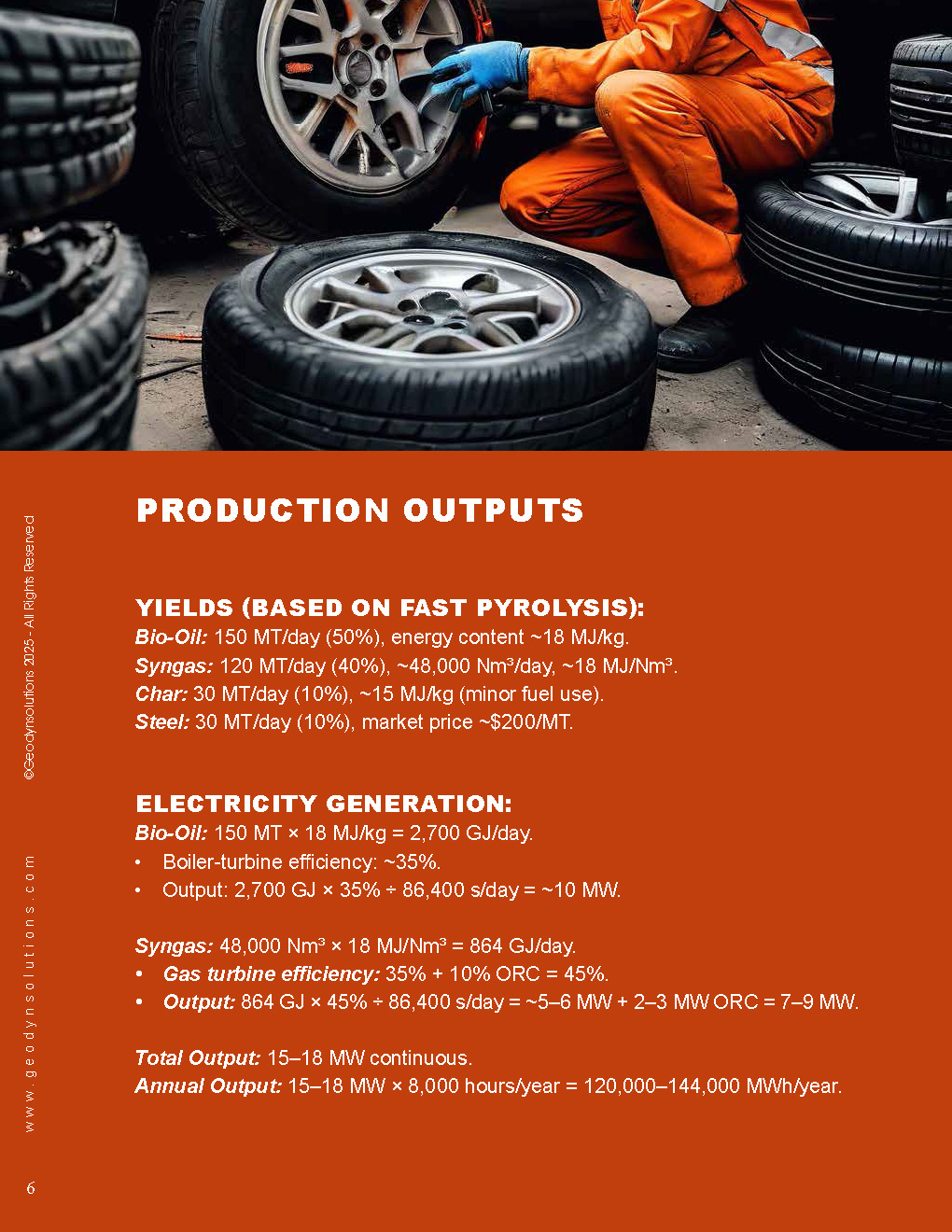
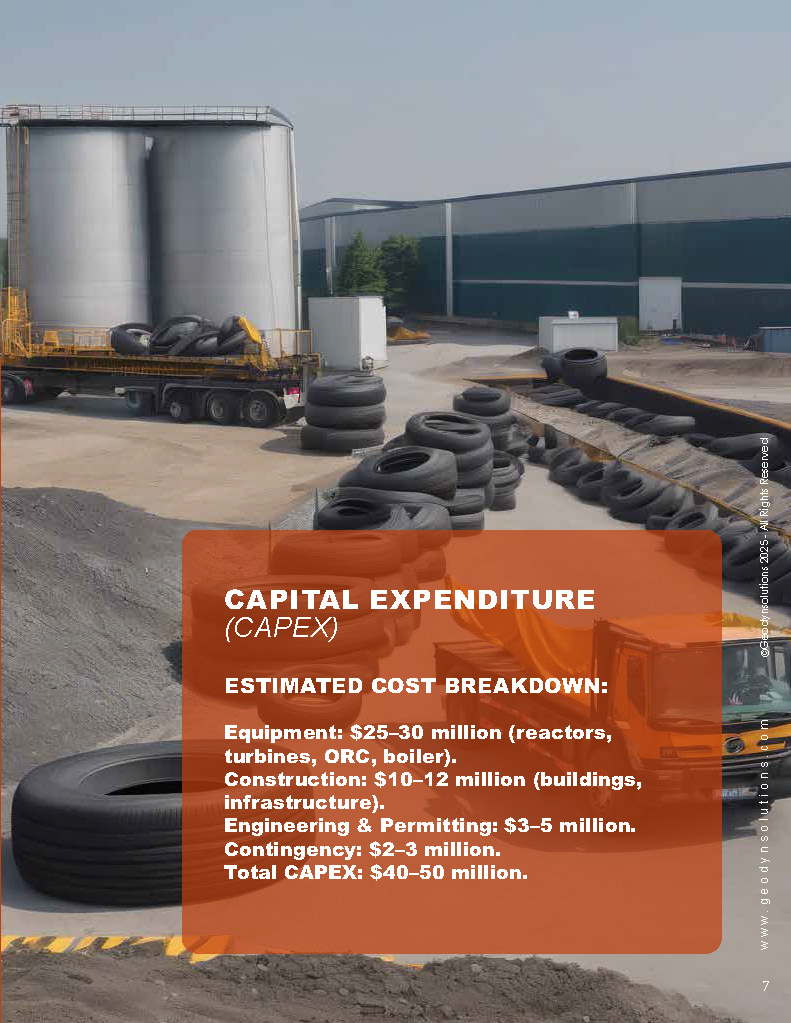
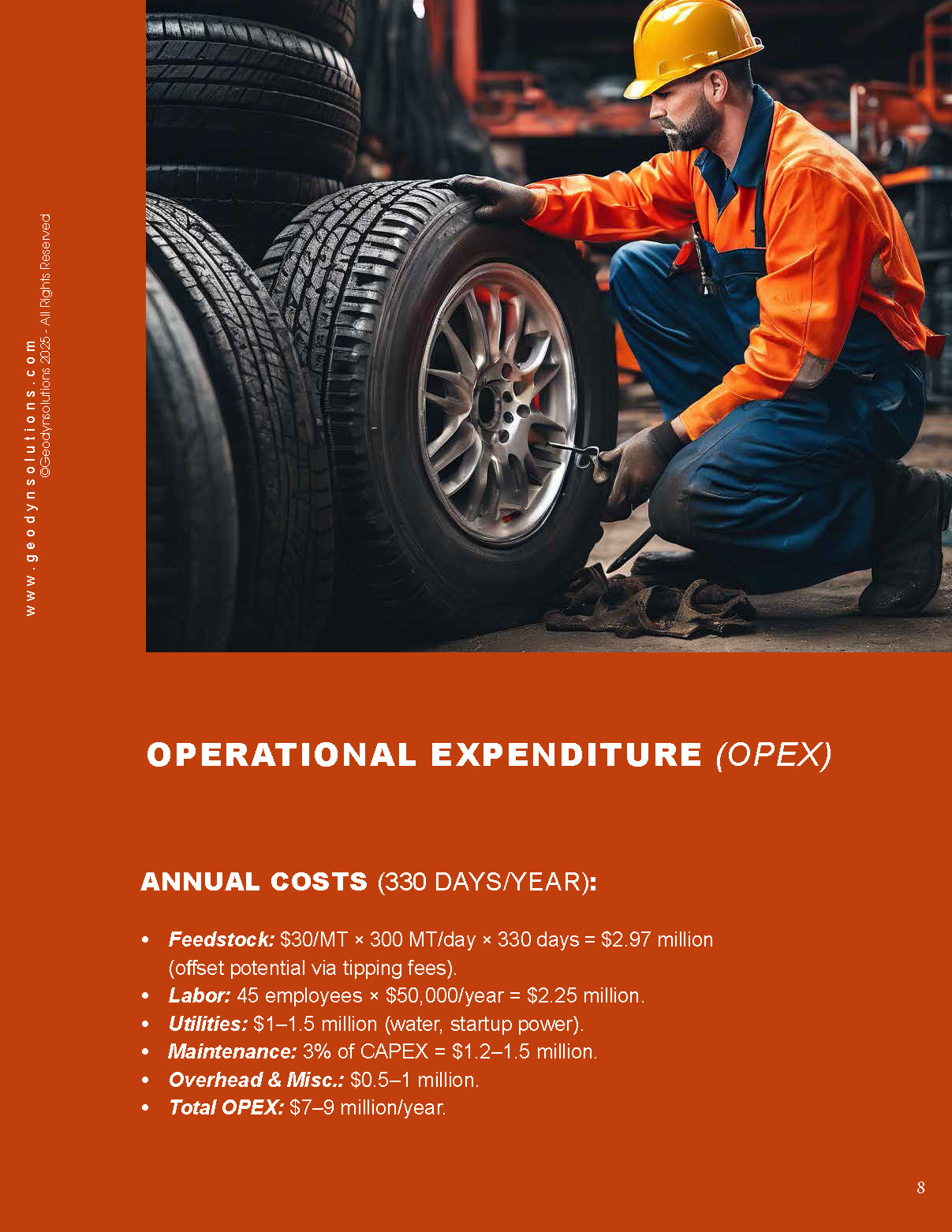
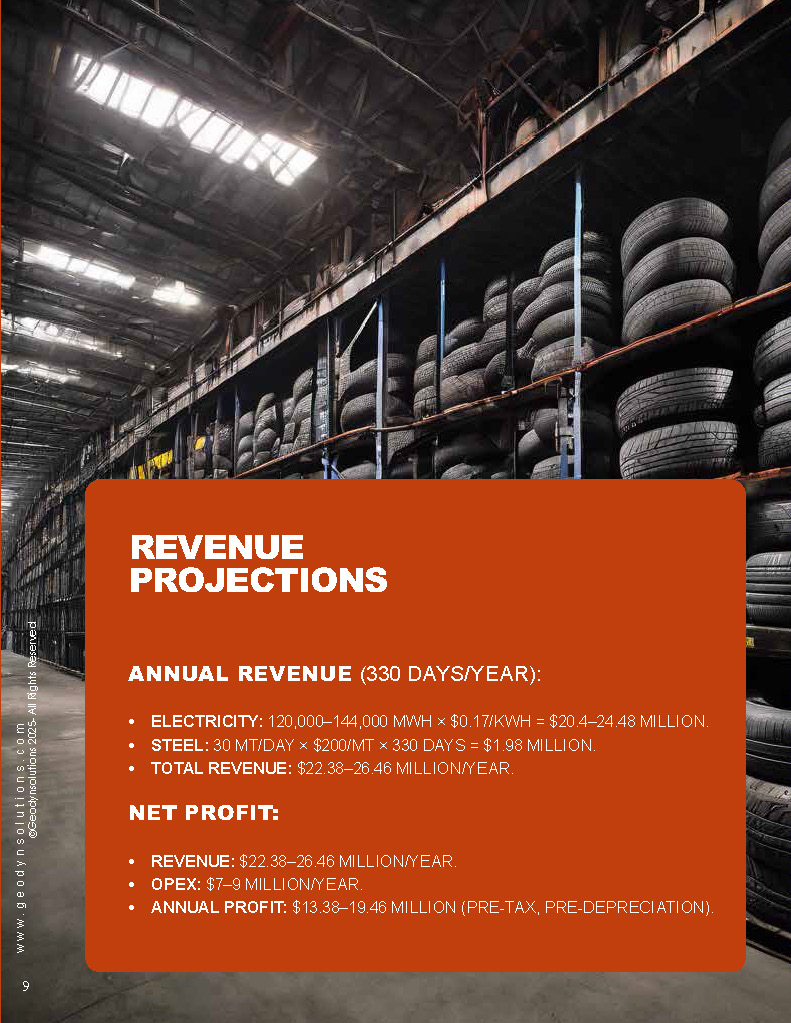
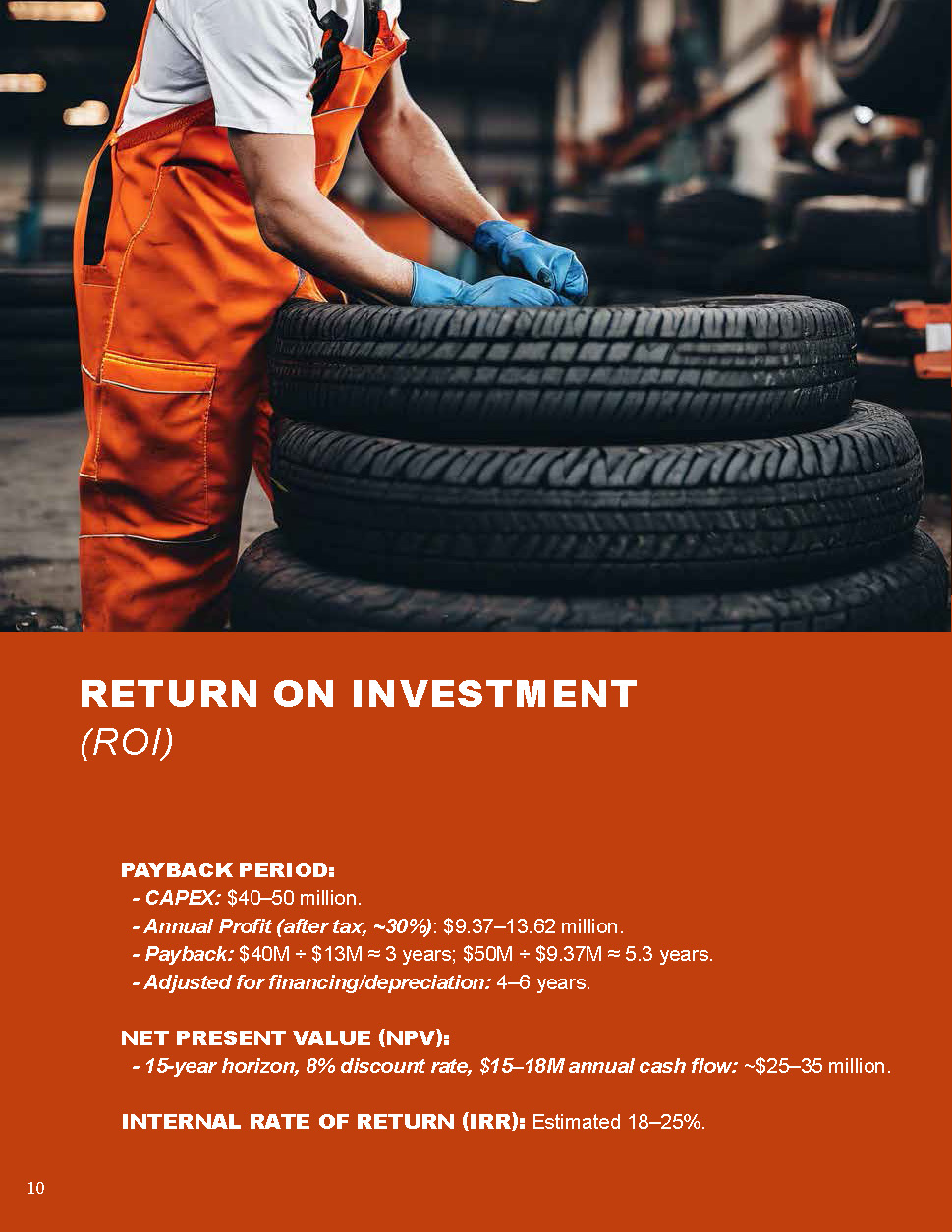
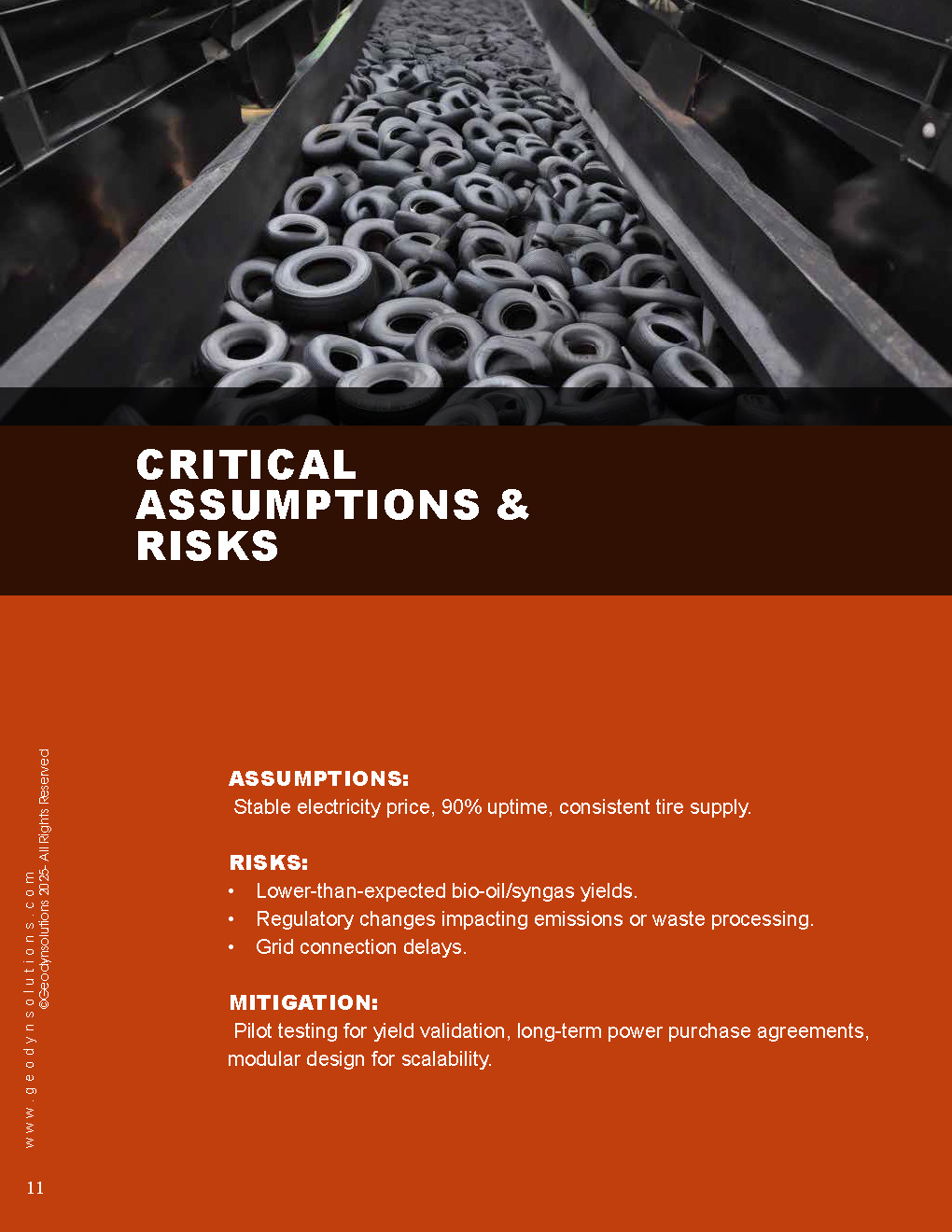
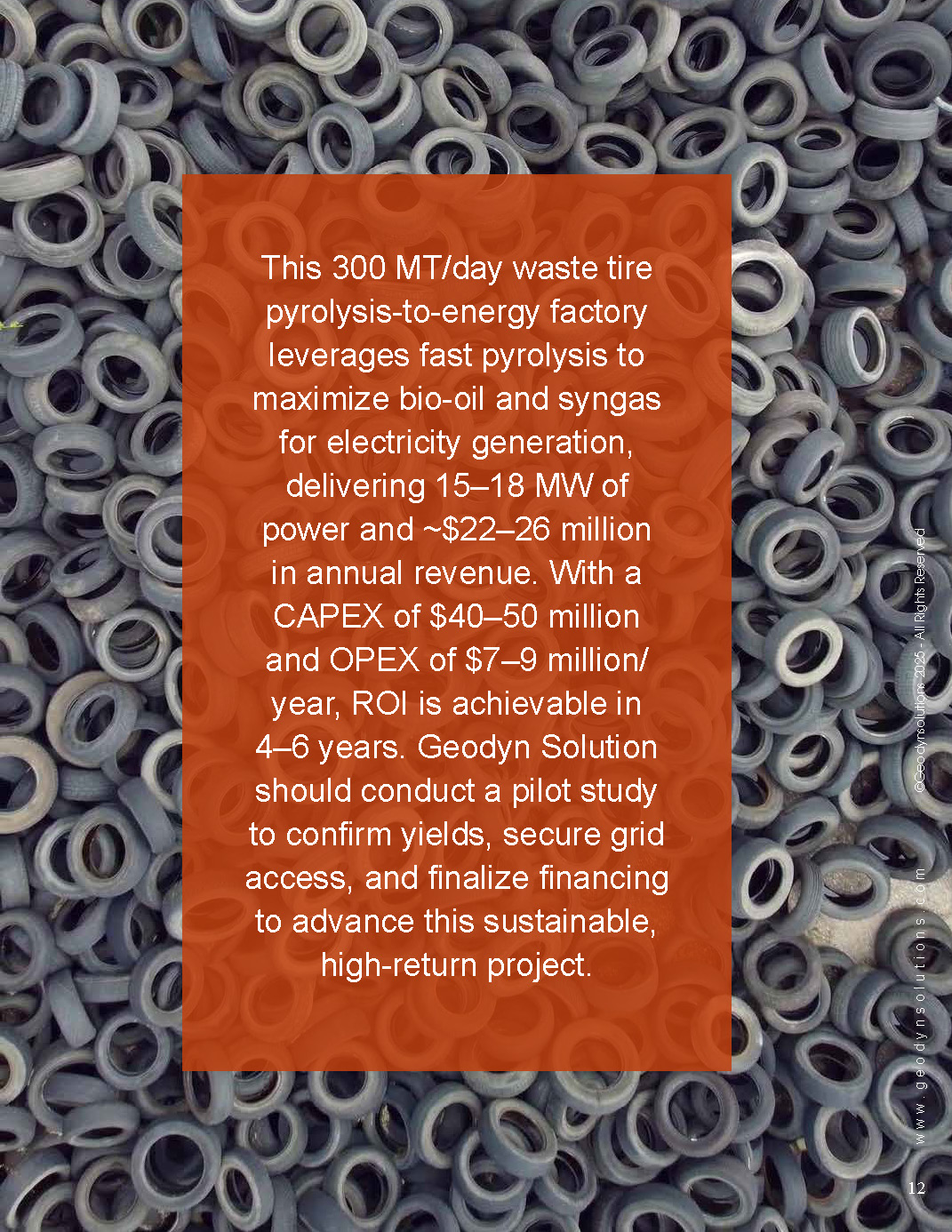
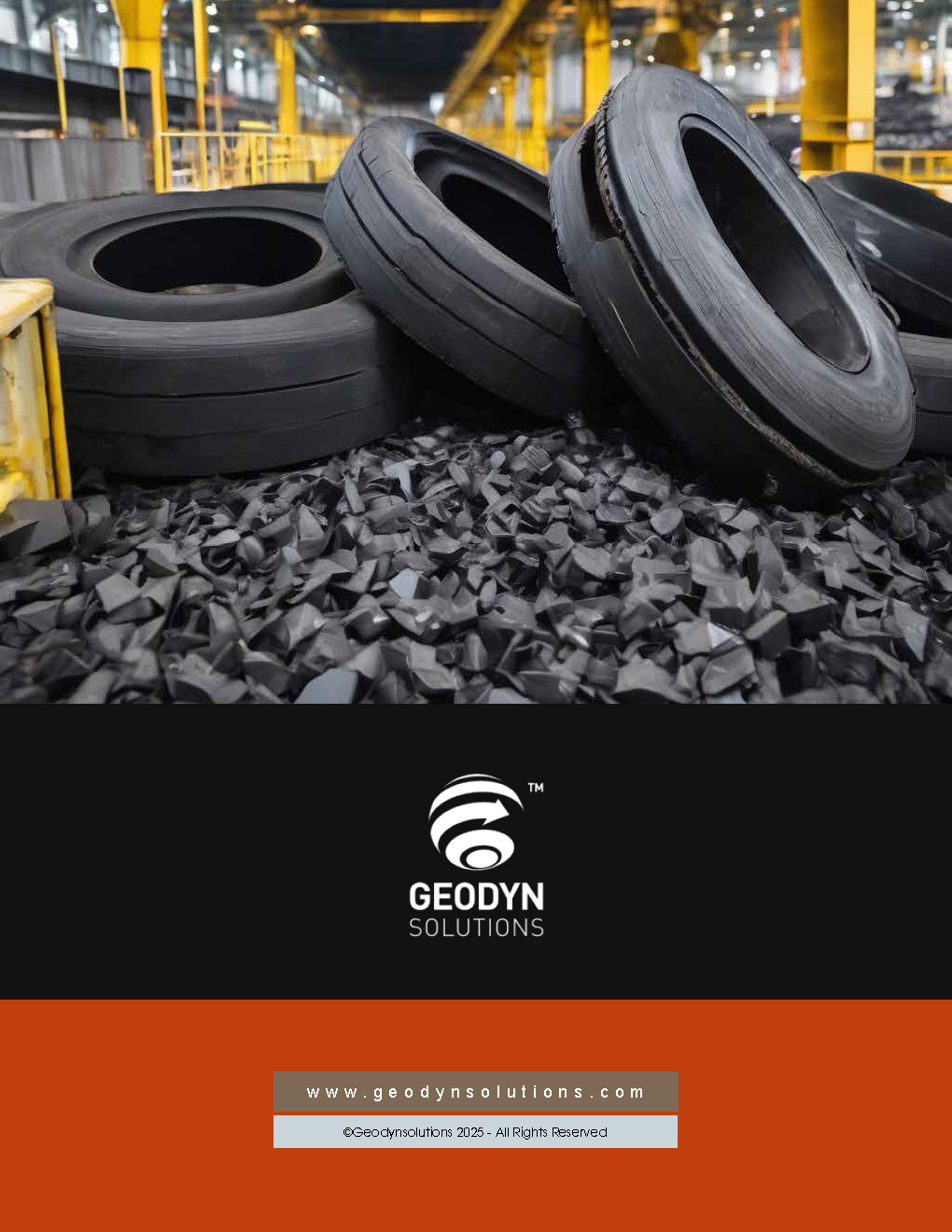